Best Free 3d Printer Design Software
- Best 3d Free Modeling Software
- Best Free 3d Printer Design Software
- 3d Modeling Software For Beginners
- Best Free 3d Printer Modeling Software
Find the whole range of programmatic, parametric, sculpting and 3D modeling software. 3D printing design tools for both the Beginner and Professional.
The number and variety of 3D software packages on the market is staggering, but many of the top applications in use by commercial film, gaming, and effects studios cost hundreds or thousands of dollars.
- We scored and ranked the 20 best 3D printing software. Begin typing your search above and press return to search. Press Esc to cancel. Most Popular 3D Modeling & Design Software for 3D Printing (2017 Update) by Fabian May 9, 2017. A free 3D editing.
- A comprehensive list of 3D Printing Software - includes all software required to create a 3D model, prepare and 3D print it. To use 3D design and printing.
It's true that most commercial applications offer time-limited free trials or abbreviated learning editions for students and hobbyists. If you're planning to work in the computer graphics industry one day, these are well worth exploring even if you can't afford a full license, because your skills in the commercial packages are what will ultimately land you a job.
However, plenty of free 3D software suites are out there for hobbyists, independent filmmakers who don't have the budget for expensive software, and budget-conscious freelance professionals who have found all the tools and power they need in cost-free solutions like Blender or SketchUp.
Just because the software is free doesn't necessarily make it any less valuable. This list isn't exhaustive. There are dozens of other free 3D tools available beyond those mentioned here. However, these are the strongest of the bunch.
Blender
What We Like
Interface vastly improved over early versions.
Great for video games and animation.
Nearly on par with expensive professional 3D modeling programs.
What We Don't Like
Less useful in designing architecture and objects like furniture.
Heavy use of shortcuts to execute commands can be daunting for new users learning the software.
Blender is easily the most versatile entry on this list, and in many regards, it compares favorably to top digital content creation tools like Cinema 4D, Maya, and 3Ds Max. To this day, it stands as one of the greatest open-source development projects ever conceived.
Blender is full-featured, offering a complete range of modeling, surfacing, sculpting, painting, animation, and rendering tools.
The software is good enough to have produced numerous impressive short films and is in use by several professional studios.
Blender was criticized early on for having a confusing interface, but don't let outdated complaints steer you away. The software was given a thorough overhaul recently and emerged with a fresh interface and a feature set that aims for parity with the best.
While you don't see Blender in any Hollywood effects pipelines where Autodesk and Houdini are deeply ingrained, Blender has steadily carved out a niche in motion graphics and visualization, similar to where Cinema 4D excels.
Pixologic Sculptris
What We Like
Best 3d Free Modeling Software
Makes quick editing easy.
Excellent tool for learning the art.
Users can transition to ZBrush without a difficult learning curve.
What We Don't Like
Rendering can be slow at times.
Lacks some useful tools and features found in other software.
Sculptris is a digital sculpting application similar to ZBrush or Mudbox, but with an easier learning curve. Because Sculptris uses dynamic tessellation, it is essentially geometry-independent, meaning it is an ideal learning package for someone with few or no modeling skills who wants to try his hand at sculpting. Sculptris was originally developed independently by Tomas Pettersson, but is now owned and maintained by Pixologic as a free counterpart to ZBrush. Sculptris is aimed at beginners. The website offers video tutorials and an assurance that the skills you learn in Sculptris easily translate to ZBrush.
Sculptris was last updated in 2011. Pixologic still allows downloads but warns that as legacy software, it's no longer maintained or supported.
SketchUp
What We Like
Great for architectural modeling.
Large library of models available.
What We Don't Like
Software user guide. Interface may be a challenge for new users to get used to.
Importing 3D models created in other programs can sometimes be a problem.
SketchUp is an intuitive and accessible modeler, originally developed by Google and now owned by Trimble. SketchUp excels at practical and architectural design and probably has more in common with a CAD package than traditional surface modelers like Maya and Max.
Like Blender, SketchUp has been amazingly well received and has gradually carved out a niche with professionals in the visualization field due to its ease of use and speed.
The software has little in the way of organic modeling tools, but if your primary interest is in architectural modeling, SketchUp is an excellent starting point. You begin by drawing lines and shapes and then stretch and copy them to make whatever you like. You don't have to draw everything, though. SketchUp offers an enormous library of free 3D models to get you started — search the 3D Warehouse for what you need.
Wings 3D
What We Like
Good tool for learning 3D modeling basics.
Supports many other 3D file formats.
What We Don't Like
Doesn't offer features beyond the basics.
No animations.
Wings is a straightforward open-source subdivision surface modeler, which means it has similar modeling capabilities to Maya and Max but none of their other functions.
Because Wings uses traditional (standard) polygon modeling techniques, everything you learn here is applicable in other content-creation packages, making this an ideal starting point for anyone looking to learn how to model for animation, film, and games.
Tinkercad
What We Like
Easy-to-learn interface.
Design tools are online, no software to download.
What We Don't Like
Best Free 3d Printer Design Software
Doesn't fare well with very complex designs.
Requires an internet connection.
Tinkercad is an impressive suite of free, lightweight 3D tools offered by Autodesk as an easy entry point into the world of 3D. Autodesk develops five different applications under the Tinkercad banner, including modeling and sculpting apps, an iPad based creature designer, and a tool to assist with fabrication and 3D printing.
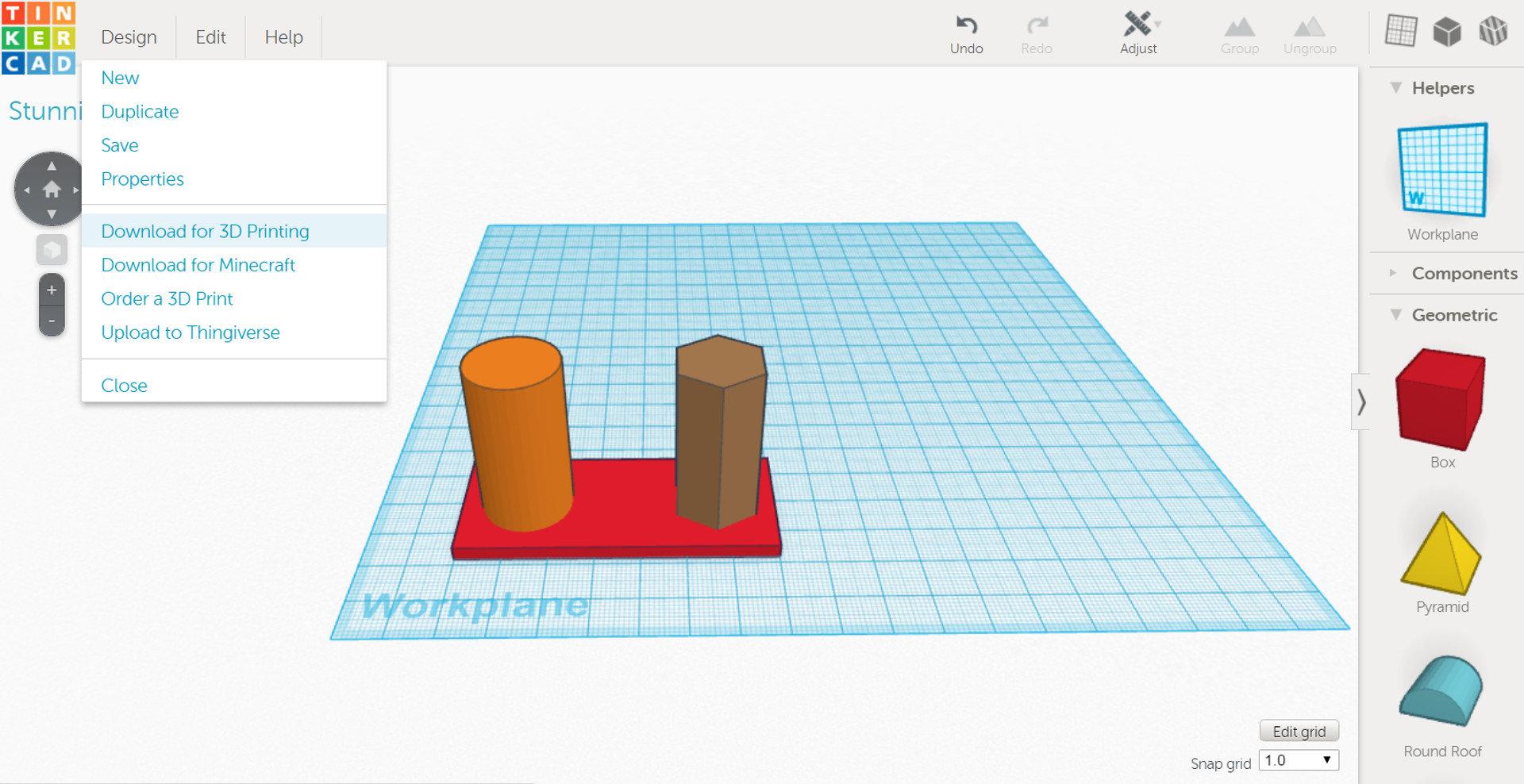
In a way, Tinkercad is AutoDesk's answer to Sculptris and Sketchup and is meant to interest beginners in 3D without the tremendous learning curve of their Autodesk's flagship applications: CAD, Maya, Max, and Mudbox.
Daz Studio
What We Like
Includes lots of props and models to use.
Strong in animation, image, and film creation tasks.
What We Don't Like
Limited sculpting, modeling, and surfacing tools.
Easier to create new models in other 3D software and import for use.
Daz Studio is an image creation tool that comes with a wealth of characters, props, creatures, and buildings that you can arrange and animate to create still images or short films. The software is primarily meant for users who want to create 3D images or films without the overhead of creating all their models and textures by hand.
The software's animation and rendering toolset is fairly robust, and in the right hands, users can create impressive shots. However, without a full range of modeling, surfacing, or sculpting tools built in, your content can become limited unless you're willing to buy 3D assets in the Daz marketplace or create them yourself with a third-party modeling package.
Still, it's a great piece of software for people who just want to jump in and create a 3D image or film without a whole lot of overhead.
3d Modeling Software For Beginners
Mandelbulb 3D
What We Like
Create impressive fractal objects and scenes.
Can play around with formulas to see what you get.
The website offers downloadable examples to experiment with.
What We Don't Like
Takes some time to acclimate to this software.
Interface is overwhelming at first and not as intuitive as other 3D software.
If you're interested in fractals, Mandelbulb 3D should be right up your alley. The application certainly takes some getting used to, but the result is stellar once you know what you're doing. The 3D fractal environment includes color, lighting, specularity, depth-of-field, and shadow and flow effects used to generate amazing fractal objects. If the concept of fractals is Greek to you, visit the featured artists' section of the Mandelbulb website to see the types of things you can do with this software.
Autodesk Software (Free but Limited)
What We Like
Free top-tier 3D design software if used only non-commercially.
Powerful and feature-rich software tools that are industry standards.
What We Don't Like
Steep learning curve when starting to use these complex software packages.
Software can have hefty system requirements and be resource intensive.
Autodesk offers virtually its entire software line free for non-commercial use to 'students and community members.' However, you don't have to be enrolled in a school to download them. If you want to work in the industry eventually, knowing Autodesk software is a valuable skill, so this is a highly recommended path. The only limitation is that you can't use any of the software in commercial projects. Among the educational downloads are 3DS Max, Maya, Inventor Professional, and AutoCAD.
3D Printing: Not Just for Professionals
Barely a decade ago, 3D printers were hulking, expensive machines reserved for factories and well-heeled corporations. They were all but unknown outside the small circles of professionals who built and used them. But thanks largely to the RepRap open-source 3D printing movement, these amazing devices have become viable and affordable products for use by designers, engineers, hobbyists, schools, and even curious consumers.
If you're in the market for one, it's important to know how 3D printers differ from one another so you can choose the right model. They come in a variety of styles, and may be optimized for a particular audience or kind of printing. Preparing to take the plunge? Here's what you need to consider.
What Do You Want to Print?
Tied into the matter of what you want to print is a more fundamental question: Why do you want to print in 3D? Are you a consumer interested in printing toys and/or household items? A trendsetter who enjoys showing the latest gadgetry to your friends? An educator seeking to install a 3D printer in a classroom, library, or community center? A hobbyist or DIYer who likes to experiment with new projects and technologies? A designer, engineer, or architect who needs to create prototypes or models of new products, parts, or structures? An artist who seeks to explore the creative potential of fabricating 3D objects? Or a manufacturer, looking to print plastic items in relatively short runs?
Your optimal 3D printer depends on how you plan to use it. Consumers and schools will want a model that's easy to set up and use, doesn't require much maintenance, and has reasonably good print quality. Hobbyists and artists may want special features, such as the ability to print objects with more than one color, or to use multiple filament types. Designers and other professionals will want outstanding print quality. Shops involved in short-run manufacturing will want a large build area to print multiple objects at once. Individuals or businesses wanting to show off the wonders of 3D printing to friends or clients will want a handsome yet reliable machine.
For this guide, we will focus on 3D printers in the sub-$4,000 range, targeted at consumers, hobbyists, schools, product designers, and other professionals, such as engineers and architects. The vast majority of printers in this range build 3D objects out of successive layers of molten plastic, a technique known as fused filament fabrication (FFF). It is also frequently called Fused Deposition Modeling (FDM), although that term is trademarked by Stratasys, Inc. A few use stereolithography—the first 3D printing technique to be developed—in which ultraviolet (UV) lasers trace a pattern on a photosensitive liquid resin, hardening the resin to form the object.
What Size Objects Do You Want to Print?
Make sure that a 3D printer's build area is large enough for the kind of objects that you intend to print with it. The build area is the size, in three dimensions, of the largest object that can be printed with a given printer (at least in theory—it may be somewhat less if the build platform is not exactly level, for example). Typical 3D printers have build areas between 6 and 9 inches square, but they can range from a few inches up to more than 2 feet on a side, and a few are actually square. In our reviews, we provide the build area in inches, in height, width, and depth (HWD).
What Materials Do You Want to Print With?
Most lower-priced 3D printers use the FFF technique, in which plastic filament, available in spools, is melted and extruded, and then solidifies to form the object. The two most common types of filament by far are acrylonitrile butadiene styrene (ABS) and polylactic acid (PLA). Each has slightly different properties. For example, ABS melts at a higher temperature than PLA and is more flexible, but it emits fumes when melted that many users find unpleasant, and it needs a heated print bed. PLA prints look smooth, but they tend to be on the brittle side.
Other materials used in FFF printing include, but are not limited to, high-impact polystyrene (HIPS), wood, bronze, and copper composite filaments, UV-luminescent filaments, nylon, Tritan polyester, polyvinyl alcohol (PVA), polyethylene terephthalate (PETT), polycarbonate, conductive PLA and ABS, plasticized copolyamide thermoplastic elastomer (PCTPE), and PC-ABS. Each material has a different melt point, so use of these exotic filaments is limited to printers designed for them, or ones with software that lets users control the extruder temperature.
Filament comes in two diameters—1.85mm and 3mm—with most models using the smaller-diameter filament. Filament is sold in spools, generally 1kg (2.2 pounds), and sells for between $20 and $50 per kilogram for ABS and PLA. Although many 3D printers will accept generic spools, some companies' 3D printers use proprietary spools or cartridges. Make sure that the filament is the right diameter for your printer, and that the spool is the right size. In many cases, you can buy or make (even 3D print) a spool holder that will fit various spool sizes. (For much more on 3D printing filaments, check out our filament explainer.)
Stereolithography printers can print at high resolutions and eschew filament in favor of photosensitive (UV-curable) liquid resin, which is sold in bottles. Only a limited color palette is available: mainly clear, white, gray, black, or gold. Working with liquid resin and isopropyl alcohol, which is used in the finishing process for stereolithography prints, can be messy.
How High of a Resolution Do You Need?
A 3D printer extrudes successive thin layers of molten plastic in accordance with instructions coded in the file for the object being printed. For 3D printing, resolution equals layer height. Resolution is measured in microns, with a micron being 0.001mm, and the lower the number, the higher the resolution. That's because the thinner each layer is, the more layers are needed to print any given object, and the finer the detail that can be captured. Note, however, that increasing the resolution is sort of like increasing a digital camera's megapixel count: Although a higher resolution often helps, it doesn't guarantee good print quality.
Nearly all 3D printers being sold today can print at a resolution of 200 microns—which should produce decent-quality prints—or better, and many can print at 100 microns, which generally delivers good-quality prints. A few can print at higher resolutions still, as fine as 20 microns, but you may have to go beyond the preset resolutions and into custom settings to enable resolutions finer than 100 microns.
Higher resolution comes at a price, as you'll usually pay a premium for printers with resolutions higher than 100 microns. Another downside of increasing the resolution is that it can add to print times. Halving the resolution will roughly double the time it takes to print a given object. But for professionals who require the highest quality in the objects they print, the extra time may be worth it.
The field of 3D printing for consumers and hobbyists is still in its infancy. The technology has been evolving at a rapid rate, making these products ever more viable and affordable. We can't wait to see what improvements the coming years bring.
Do You Want to Print in Multiple Colors?
Some 3D printers with multiple extruders can print objects in two or more colors. Most are dual-extruder models, with each extruder being fed a different color of filament. One caveat is that they can only print multicolored objects from files that have been designed for multicolor printing, with a separate file for each color, so the areas of different colors fit together like (three-dimensional) jigsaw puzzle pieces.
What Surface Should You Build On?
The importance of the build platform (the surface on which you are printing) may not be apparent to 3D printing newbies, but it can prove critical in practice. A good platform will let an object adhere to it while printing, but it should allow for easy removal when the printing is done. The most common configuration is a heated glass platform covered with blue painter's tape or a similar surface. Objects stick to the tape reasonably well, and they are easy to remove when completed. Heating the platform can prevent the bottom corners of objects from curling upward, which is a common issue, especially when printing with ABS.
With some build platforms, you apply glue (from a glue stick) to the surface, to give the object something on which to adhere. This is workable, as long as the object can easily be removed after printing. (In some cases, you have to soak both platform and object in warm water for the object to come loose.)
A few 3D printers use a sheet of perforated board with tiny holes that fill with hot plastic during printing. The trouble with this method is that although it will hold an object solidly in place during printing, the object may not easily come loose afterward. Using a thumbtack or an awl to push the plugs of hardened plastic out of the perforations to free the object and/or clean the board is a time-consuming process, and can damage the board.
If the build platform becomes tilted, it can impede printing, particularly of larger objects. Most 3D printers offer instructions on how to level the build platform, or provide a calibration routine in which the extruder moves to different points on the platform to ensure that the points are all at the same height. A small but growing number of 3D printers automatically level the build platform.
Setting the extruder at the proper height above the build platform when commencing a print job is also important for many printers. Such 'Z-axis calibration' is usually performed manually, by lowering the extruder until it's so close to the build platform that a sheet of paper placed between extruder and platform can move horizontally with slight resistance. A few printers automatically perform this calibration.
Do You Need a Closed Frame?
Closed-frame 3D printers have an enclosed structure with a door, walls, and a lid or hood. Open-frame models provide easy visibility of print jobs in progress, and easy access to the print bed and extruder. A closed-frame model is safer, keeping kids and pets (and adults) from accidentally touching the hot extruder. And it also means quieter operation, reducing fan noise and possible odor, especially when printing with ABS, which can exude a burnt-plastic smell.
How Do You Want to Connect to the Printer?
With most 3D printers, you initiate the printing from a computer via a USB connection. Some printers add their own internal memory, which is an advantage because they can keep a print job in memory and continue printing even if the USB cable is disconnected or the computer is shut down. A few offer wireless connectivity, either via 802.11 Wi-Fi or a direct, peer-to-peer link. A downside of wireless is that, because 3D printing files can be up to 10MB in size, it can take much longer to transfer them. Another connection method that we have seen is Ethernet.
Many 3D printers have SD card slots from which you can load and print 3D object files using the printer's controls and display, while others have ports for USB thumb drives. The advantage of printing directly from media is that you don't need a computer. The downside is that they add an extra step, in transferring the files to your card. Typically, wireless, SD card, or USB thumb-drive connectivity is offered in addition to the basic USB cable, although a few models offer one or more of those options.
What Software Do You Need?
Today's 3D printers come with software on a disk or as a download. It's Windows-compatible, and in many cases can work with macOS and Linux as well. Not long ago, 3D printing software consisted of several parts, including a printing program that controlled the motion of the extruder, a 'healing' program to optimize the file to be printed, a slicer to prepare the layers to be printed at the proper resolution, and the Python programming language.
Best Free 3d Printer Modeling Software
These components were derived from the RepRap open-source tradition, which was what spurred the development of low-cost 3D printers. But today, manufacturers of 3D printers have integrated these programs into seamless, user-friendly packages. Some 3D printers also allow you to use separate component programs, if you prefer.
Ready for Our Recommendations?
Below are the best 3D printers that we've reviewed recently. They cover a wide range in price, features, and printing methods, but they all represent quality. For more information on what 3D printing is, and how it works, our 3D-printing primer is a good place to start. And be sure to check out our roundup of the best overall printers.
Best 3D Printer Reviews Featured in This Roundup:
Dremel DigiLab 3D45 3D Printer Review
MSRP: $1799.00Pros: Very good print quality. Easy to use. User-friendly yet powerful software. Prints via USB, Ethernet, and Wi-Fi, and from a USB thumb drive. Safe design. Relatively quiet.
Cons: Limited filament colors compared with competitors.Touch screen is not particularly responsive.
Bottom Line: The Dremel DigiLab 3D45 is featured-packed, prints accurately, and comes loaded with powerful software, making it one of the best 3D printers we've tested.
Read ReviewFormlabs Form 2 Review
MSRP: $3499.00Pros: Superb print quality. Automatic resin feed. USB, Wi-Fi, and Ethernet connectivity. Touch screen. Several custom resin types available.
Cons: Printer couldn't detect one resin cartridge in our testing. A few confusing error messages. Takes time to master printing.
Bottom Line: The Form 2 offers magnificent print quality, a good selection of resins, and an improved user experience over the previous generation of Formlabs 3D printers.
Read ReviewMakerBot Replicator+ Review
MSRP: $2499.00Pros: Easy to use. Very good print quality. User-friendly yet powerful software. Prints via USB, Ethernet, and Wi-Fi, and from a USB thumb drive. Safe design for an open-frame printer. Relatively quiet.
Cons: Printer setup through MakerBot Mobile app can be tricky. Somewhat pricey filament.
Bottom Line: The MakerBot Replicator+ 3D printer is a marked upgrade over its predecessor, offering better speed, a larger build area, and workflow solutions for professionals.
Read ReviewUltimaker S5 Review
MSRP: $5995.00Pros: Dual extruders. Large build volume. Quiet. Good print quality. Easy setup and operation. Touch screen.
Cons: Pricey. Relatively slow printing at default resolution.
Bottom Line: The Ultimaker S5's dual extruders, good print quality, large build volume, and easy setup and operation make it worthy of our Editors' Choice as a professional-grade filament-based 3D printer.
Read ReviewDremel DigiLab 3D40 Flex 3D Printer Review
MSRP: $1299.00Pros: Simple setup. User-friendly software. Solid print quality. Flexible build plate makes object removal easy. Multiple connection choices.
Cons: Limited to PLA filament.
Bottom Line: Dremel's easy-to-use DigiLab 3D40 Flex 3D Printer has user-friendly software, good output quality, and a wide mix of connectivity options. It's a fine choice for classroom use.
Read ReviewLulzBot Mini 2 Review
MSRP: $1500.00Pros: Easy to set up and use. Powerful software. Quiet operation. Supports a variety of filament types. LCD with SD-card slot. Self-leveling print bed. Easy to remove finished objects from print bed. Works with Windows, macOS X, and Linux.
Cons: Print quality inconsistent at times. No bundled filament. Open frame increases risk of burns from a hot extruder. Relatively sparse connectivity options.
Bottom Line: The LulzBot Mini 2 is easy to use and works with a variety of filament types. It's a good choice for schools and hobbyists, and anyone willing to invest in a powerful and versatile 3D printer.
Read ReviewUltimaker 3 Review
MSRP: $3495.00Pros: Easy to use. Strong print quality. Reliable, misprint-free printing. Dual extruders let you print with two colors or filament types. Quiet. Several connection choices.
Cons: Long print times at default resolution.
Bottom Line: The Ultimaker 3 has very good print quality for a 3D printer that prints with plastic filament, and its dual print cores let you print using two filament types or colors.
Read ReviewXYZprinting da Vinci Jr. 2.0 Mix Review
MSRP: $449.95Pros: Low price for a two-color 3D printer. Good print quality. No misprints. Quiet. Prints over a USB or Wi-Fi connection, or from an SD card.
Cons: Poor documentation makes the learning curve longer than it should be. Requires use of proprietary filament.
Bottom Line: The XYZprinting da Vinci Jr. 2.0 Mix is great choice for a low-price consumer 3D printer, especially if you want to print in two colors.
Read ReviewFlashforge Finder 3D Printer Review
MSRP: $499.00Pros: Quiet. Good print quality. Connects via USB 2.0 cable, USB thumb drive, or Wi-Fi. Reasonably priced.
Cons: Some objects pulled off the platform during testing. Poor documentation. Modest build volume. Limited to printing with polylactic acid filament (PLA).
Bottom Line: The Flashforge Finder 3D Printer is moderately priced and offers good print quality, but it proved tricky to get up and running in our tests.
Read ReviewMonoprice Voxel 3D Printer Review
MSRP: $399.99Pros: Easy to set up and use. Budget price for printer and filament spools. Supports PLA, ABS, and several composite filament types. Versatile software. Prints over Ethernet or Wi-Fi, or from a USB thumb drive.
Cons: Frequent misprints on certain test objects. Slightly balky touch screen.
Bottom Line: The Monoprice Voxel is an under-$400 3D printer that's easy to set up and use. It exhibits generally good print quality, but it was unable to print two of our test objects.
Read Review